The serious challenge facing today's automotive electronics engineers is to build a low-cost, fail-silent (fail-silent) automotive system that can work normally even when a failure occurs. Braking, steering, and other vehicle stability control functions are mission-critical features that have extremely high safety requirements. Even though electronic chassis control technology is increasingly popular with the public, it cannot easily meet the above challenges.
For the main automotive system functions, the electronic chassis management technology has great appeal, but for various reasons, the technology is still difficult to implement, and it still faces many difficulties in terms of safety and reliability. In order to meet the current safety regulations, the International Electrotechnical Commission (IEC) has defined relevant standards for the functional safety of electrical / electronic / programmable electronic safety-related systems. Currently, IEC 61508 is regarded as the highest level standard in the development of safety-critical systems. Although the standard has not yet been fully enforced in the form of law, it is still hoped that automotive system designers can meet this actual technical standard. Designers of automotive systems must consider the requirements of the entire signal chain from input sensors to digital processing and transmission when constructing application functional safety.
IEC 61508 takes "danger" and "risk analysis" as part of the system design, and defines the "functional safety" of the Electronic Control Unit as "part of the overall safety-depending on whether the system or equipment can Respond correctly to its input ". As shown in Figure 1. Each safety function of the system is evaluated on the basis of "requirements" (what work the function needs to complete) and "integrity" (the possibility of performing the function satisfactorily). In addition, the standard further divides the probability of a dangerous failure of a safety function in a high-intensity working mode or continuous working mode into four different "safety integrity levels" (SIL). Each level covers a range of acceptable failure rates, which is the "mean time between failures" (MTTF), and SIL4 is the most stringent standard. SIL ratings are applicable to many industries, including the automotive industry, and the definition of each SIL rating applies to their respective industry sectors. SIL2 and SIL3 in the safety integrity level are the most common safety levels in non-road applications.

Figure 1 The functional safety of the overall system relies on the device to respond to input for normal work
Depending on the safety function and importance, automotive systems can comply with SIL2 or SIL3 regulations under the IEC 61508 standard. The reliability of the self-detection system requires that the "safety failure factor" (SFF) obtained by multi-level statistics reaches 99%, and the specific calculation method of the reliability parameter is the ratio of the detected dangerous failures (including non-dangerous failures) to all failures. "Diagnosis Coverage Rate" (DC) refers to the ratio of detected dangerous failures to all dangerous failures. In addition, for safety-critical automotive systems, DC should reach 99%.
Whether or not to pass the SIL3 certification of the automotive system usually depends on the performance of the electronic control unit (ECU) that starts and controls the mechanical system. Independent safety assessment agencies such as TUV Rheinland are responsible for ECU assessment and SIL3 certification of automotive systems. TUV is an international service group that can issue safety and quality certificates for products, systems and services.
Mission-critical integrated mechanical systems (such as braking) cannot be completely replaced by electronic products. However, any advanced mechanical or electronic safety required by the SIL3 certification needs to be achieved through the use of a redundant system, which helps the widespread implementation of redundancy.
SIL3 certification of electronic subsystem
Replacing hydraulic or mechanical systems with electronic systems will inevitably benefit OEMs, automakers and consumers. The electronic system can eliminate the burden of the belt drive of the internal combustion engine, thereby helping to reduce cost, weight and fuel consumption.
Automobile manufacturers can replace hydraulic brake boosters with mechanical solutions, and eventually cancel the hydraulic transmission system completely to achieve a fully electronically controlled wire-controlled braking system, as shown in Figure 2. However, this revolutionary change requires the implementation of redundant systems or backup systems (similar to avionics systems) in order to avoid the risk that the vehicle will completely lose its braking ability at a dangerous moment. The excessive steps during this period include the "hybrid braking" mode, which means that only one hydraulic backup system can be installed on one of the vehicle's axles instead of two.
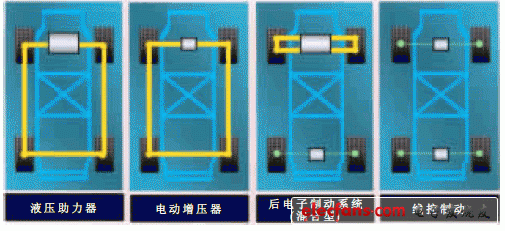
Figure 2 Replacing hydraulic boosters with electrical solutions helps significantly reduce fuel consumption, cost and noise
Microprocessor (MCU) is a key component in ECU. It is impossible to achieve SIL3 certification requirements using traditional automotive MCUs. A new chip architecture is required to ensure the processing results, data integrity of bus traffic, and the safety and reliability of data in memory, while meeting strict response time requirements.
According to the IEC 61508 standard, the causes of dangerous failures include the following factors:
(1) The software or hardware system specifications are incorrect;
(2) Missing safety requirements specifications;
(3) Random hardware failure;
(4) System cause failure;
(5) Human error;
(6) Environmental impact (EMI, temperature, machinery, etc.).
From a complete system perspective, risk assessment and safety integrity requirements include the following factors:
Ensure stable power supply and clock signal integrity in the event of voltage drops, false signals, etc .; used for processing and communication redundancy or authenticity checks, including signals to and from sensors and actuators; provide fault detection functions; Provide fault management strategies, including defining safe states and fault protection in case of fault-tolerant architecture, emergency operation mode, and controllable system shutdown; enhanced software development process includes the use of formal specifications, subsets of programming languages, and code verification tools, etc. .
15.6 inch i5 5th Budget Gaming Laptop in plastic is more competitive one in device in 2022, only need around 300usd. However, 15.6 inch 500 dollar gaming laptops is one of the most important top 10 budget gaming laptops, like 14 inch i7 budget gaming laptop under 500, 15.6 inch 11th 512gb laptop, etc.
However, top budget gaming laptops also have other levels, like 15.6 inch i5 laptop 10th generation, 15.6 inch 11th generation laptop i7 512gb, etc. 2022 top laptops under 500 with 14 inch i3 i5 i7 10th you can see here also.
The custom laptop is also of updated, quality hardware, big battery, rich slots, charging by Type C, etc.
Nowadays, the hardware and mature of custom laptop is nearly no difference with brand one, so pls believe you can get a satisfy laptop for your special project, like students project, office project, gaming club etc.
Except laptop, also have custom Android Tablet, Mini PC , All In One PC, 2 In 1 Laptop , also availble.
Any other specail demand, you can contact us and share your requirements details, then matched details sended quickly.
Budget Gaming Laptop,Budget Gaming Laptop Under 500,Top Budget Gaming Laptops,Top Laptops Under 500,Top 10 Budget Gaming Laptops
Henan Shuyi Electronics Co., Ltd. , https://www.shuyicustomtablet.com