1 Introduction
MCGS (Monitor and Control Generated System) is a set of Windows-based "target =" _ blank "> Windows platform, which is used to quickly construct and generate a configuration software system for the host computer monitoring system. MCGS needs to complete the data of field devices or field instruments Acquisition and control functions must rely on the field bus to communicate with the MCGS carrier. This article mainly discusses the design and implementation of the DCS bus interface device in the MCGS system.
2 Overview
The MCGS industrial control configuration software development tool is based on the Windows operating platform, supports rapid construction and generation of industrial equipment drivers, and has good expansion capabilities. Specifically, MCGS uses AcTIve DLL components to implement device drivers, which are hooked up through a standardized OLE interface and seamlessly connected to form a whole. The device driving component and MCGS run in the same process, so the running speed is fast, the reliability is high, the data circulation is smooth, and the transmission is without delay, which meets the requirements of the monitoring system. OLE is an extensible open standard, as long as the MCGS interface specifications are followed, you can use VB, VC, Delphi and other languages ​​to compile MCGS device drivers. This provides a basis for accessing self-developed field devices and field instruments in the bus.
The rapid development of embedded technology provides a low-cost, high-performance, on-chip system with a large amount of data storage space. By connecting MAX485 and MAX232, you can easily connect the PC and DCS bus on the hardware. The computer serial port is the most commonly used communication interface when the computer communicates with other devices. A serial port can be connected to multiple communication devices (such as 255 research and communication modules can be connected to an RS 485 bus, but they share a serial port parent device), in order to adapt to the multiple operation modes of the computer serial port , MCGS adopts a communication device processing mechanism that connects multiple communication child devices under the serial communication parent device. Each child device inherits some of the public attributes of the parent device and has its own private attributes. In actual operation, MCGS provides a serial communication parent device component and multiple communication child device components. The serial communication parent device component completes the basic operation and parameter setting of the serial port, and the communication child device component is the serial port actual hook device Drivers. This provides a guarantee for connecting multiple field devices and field instruments on the bus. The interface between MCGS and DCS equipment is shown in Figure 1.
3 DCS bus interface design
3.1 MCGS interface device construction
In the system, we must first classify the field devices and field instruments. For the same type of devices, MCGS can reuse the devices and store them separately to save the time and overhead of communicating with multiple devices. The function of the interface device usually constructed should be single, and then configure it uniformly.
By constructing an interface device in MCGS, the GUI control mode of MCGS can be introduced into the control of DCS (as shown in FIG. 2) to realize the graphical, interactive and configuration of DCS control. The transformation and innovation of the equipment has good engineering application prospects and social benefits. The data shown in Figure 2 are all from field equipment, and the simulation instrument is also connected to the field instrument through DCS to achieve the control and adjustment function.
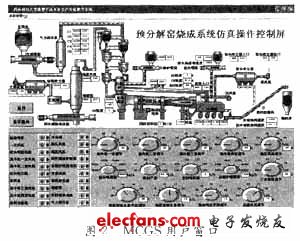
3.2 Hardware design of DCS bus interface equipment
As shown in Figure 3, the main function of the DCS gateway is to control the switching of the network (monitoring computer and control station), and he is also responsible for protocol analysis and conversion of upper and lower data communications. The DCS gateway uses Philips' LPC2136 microcontroller, which is based on a 16 / 32-bit ARM7TDMI-S CPU that supports real-time simulation and embedded tracking, and has a 256 kB embedded high-speed FLASH memory. With 2 16C550 industry standard UARTs, it can complete the communication between the upper computer and the lower computer. Contains up to 47 general-purpose I / O ports (can withstand 5 V voltage), which can be used as the enable signal of the 485 communication interface.
Multiple field devices are connected to the 485 bus. In order to avoid conflicts in the communication process, a bus-type network structure is used on the hardware, and a master-slave communication method is used on the software, that is, the host computer (MCGS) sends device I / O commands. After parsing the command, the DCS gateway selects the corresponding channel, the host computer sends a data request command, the DCS gateway directly forwards the command to the gated channel, and waits for the data to be received. Finally, the DCS gateway uploads the received data directly to the host computer. The value assigned to the corresponding variable is saved in the real-time database.
Inner Battery,Electric Bike Battery,Ebike Battery 36V 12Ah,Electric Bicycle Lithium Battery
Changxing Deli Technology Co., Ltd. , https://www.delipowers.com